熔模铸造缺陷
当前的熔模铸造企业,尤其是中小企业的技术人员严重缺失、断层;对减少、预防熔模铸造缺陷缺少思路、缺少方法、缺少经验;已经严重的制约了企业的竞争力、效率和效益,成为企业发展的瓶颈。
蜡模(也称“熔模”)制作是生产中的第一道、也是重要的一道工序,是获得优质铸件的首要条件。蜡模产生缺陷,浪费了制模的人工费用、生产时间和有效的资源;不合格的蜡模流入制壳工序,甚至浇注工序,产生了不良品。会增加工厂的生产成本、交货期,影响企业的信誉和经济效益。因此,应重视和解决蜡模缺陷。
压制熔模是用模料经过配置、压制、冷却、修模和组焊等工序组成,如图1:
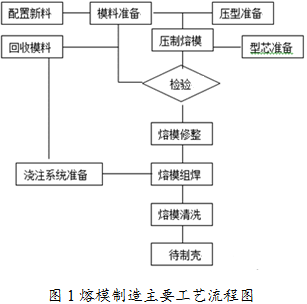
当前,压制蜡模广泛使用蜡基低温模料,或中温蜡料(如K521)。一般情况下,蜡模存在气孔、缩陷和裂纹等13种缺陷。现分述如下:
一、气孔
1.缺陷特征
蜡模的局部表面上,留有表面光滑的气穴,如图2所示。
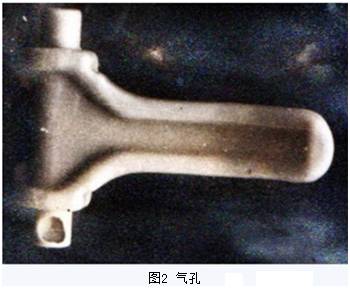
2.产生原因
(1)配置蜡料卷入过多的气体,没有充分回性处理。
生产中,配置低温蜡料常采用化蜡、刨蜡片、搅蜡膏和回性四个工序,常选用螺旋式叶片搅拌机搅拌蜡料(或“蜡膏”)。在搅拌蜡料的过程中,不可避免地卷入很多气体;并且随着搅拌机转数的增加,卷入的气体越多。尤其是蜡料搅拌后,没有进行充分的回性处理,使卷入的大量气体从蜡料中溢出,而是仍然残留在蜡料中。
(2)注蜡孔的位置不当,注蜡过程中卷入气体。
注蜡孔的位置设置不当,使蜡料在注入型腔的过程中产生涡流,卷入了过多的气体。
(3)压型设计不当,不利于型腔排气。
蜡料充满型腔的距离太长,并且型腔排气不良。
3.防止措施
(1)严格遵守蜡料配置工艺和操作规程。
配置石蜡—硬脂酸蜡料时,注意加料顺序,即先加硬脂酸,待其全部熔化后再加入石蜡或回收蜡,加热至全熔状态,其温度≤90℃。开始搅拌时,搅拌机的转数可以高些(如400r/min),蜡料温度升高后,可以降低搅拌机的转数(200~300r/min)。蜡料搅拌合适后,要进行回性处理,时间在0.5h以上,使卷入蜡料中的气体充分溢出。
(2)改进注蜡孔的位置,避免蜡料在型腔中产生紊流。
注蜡口最好设置在内浇道或有加工余量的表面上,尺寸应与压蜡机的注蜡嘴匹配;注蜡口应确保蜡料以最短的距离、平稳充满型腔,并且不产生紊流。
(3)改进压型设计,以利于排出型腔中的气体。
改进压型的设计,有利于排出型腔中的气体;必要时增设排气孔。
二、缩陷
1.缺陷特征
蜡模肥厚处出现局部收缩产生的凹陷,如图3所示。
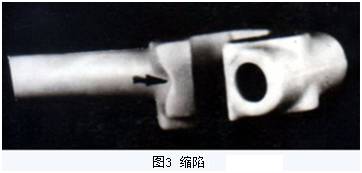
2.产生原因
(1)蜡模的厚大处(凹陷处)补缩不足。
蜡模的注射压力是制模工艺的主要参数之一。注射压力小使蜡模的厚大处(凹陷处)的收缩率大,当得不到充分的补缩时,该处产生缩陷。
保压时间是制模工艺的另一个工艺参数。蜡料充满压型型腔后,保压的时间不足,使蜡模的厚大处(凹陷处)的收缩率加大,当得不到充分的补时,造成该处蜡模缩陷。
(2)蜡模的注入量不足,补缩不充分。
注蜡孔小,或位置不当,或注蜡的压力小时,注入压型型腔的蜡料量不足,当蜡模厚大处(凹陷处)得不到充分的补缩时,造成该处蜡模缩陷。
(3)蜡模的壁厚差过大,不利于补缩。
蜡模的结构设计的不合理,壁厚差过大,不利于补缩。
(4)注蜡时蜡料的温度过高,或压型的温度过高,或两者都高。
蜡料温度高,或压型温度高,或两者都高,使蜡料的收缩率增大;当得不到充分的补缩时,而产生缩陷。
(5)蜡料的收缩率较大。
生产中使用石蜡-硬脂酸蜡料,常用58~62℃(即58号~62号)白石蜡和一级三压硬脂酸,新配置料时,各占50%。58号白石蜡的收缩率就大于62号白石蜡。石蜡-硬脂酸蜡料比石蜡-低分子聚乙烯蜡料的收缩率大。
3.防止措施
(1)增加蜡料的补缩能力。
压制蜡模时,注射压力一般选用0.2~0.5MPa。适当的提高注射压力不仅增加压型中蜡料的密度,而且可以降低蜡料的收缩率。适当的增加保压时间,一般选用(3~10)s或更长;同样可以减少蜡料的收缩率,增加蜡料的补缩能力。
(2)加大蜡料的注入量,增加补缩能力。
适当的加大注蜡孔的截面,增加单位时间内的蜡料注入量;或改变注蜡孔的位置,使蜡模的壁厚处得到充分的补缩。
(3)改进蜡模结构使其壁厚尽量均匀。
在可能的情况下,尽量使蜡模的壁厚均匀;必要时,在蜡模的肥厚处放置预先制好的冷蜡块(也称“蜡芯”),再注入蜡料形成蜡模。应根据蜡模的大小和形状,可以局部或整体放置冷蜡块。冷蜡块应该用锥形的凸台在压型中定位。凸台的高度应该根据零件的大小予以确定,一般控制在2~3mm。冷蜡块使用的蜡料应与蜡模的蜡料一致。
(4)注蜡时,控制蜡料和压型的温度。
注蜡时,对于低温蜡料一般选用蜡料温度T=48~52℃,压型的温度T=18~25℃为宜;对于中温蜡料一般选用蜡料温度T=52~60℃,压型的温度T=20~24℃为宜。
(5)选用收缩率较小的蜡料。
如当选用62℃白石蜡代替58℃白石蜡时,减少其收缩率。或提高蜡料中石蜡的含量5~10%,即55~60%,也可减少蜡料的收缩率。或采用60℃白石蜡(含量95%)与低分子聚乙烯(含量5%)配制的蜡料,其收缩率约为1%,较低。
三、裂纹
1.缺陷特征
蜡模局部裂纹,常出现在蜡模的分型面,如图4所示。
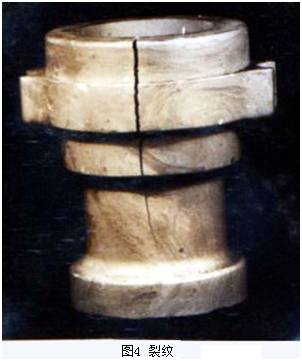
2.产生原因
(1)蜡料的收缩率大,塑性差。
采用58℃精白蜡或白石蜡与一级三压硬脂酸按照各50%配制蜡料时,蜡模的自由收缩率约为2%。当蜡料中硬脂酸的含量大于80%时,其韧性、塑性都差。易引起蜡模产生裂纹。
(2)压型,或制模间,或冷却水的温度过低。
压型的温度过低,或制模间的温度过低,或冷却水的温度过低,导致蜡模冷却过快,当蜡模收缩受阻时,易产生裂纹;或蜡模在压型中冷却的时间过长(即起模时间过长),导致蜡模收缩受阻时,易产生裂纹。
(3)蜡模结构/压型设计不合理。
蜡模结构/压型设计不合理,蜡模的壁厚不均匀,厚薄过度部分的圆角太小或呈尖角,当蜡模收缩受阻时,在其薄弱部位产生裂纹。
(4)操作不当。
起模方法不当,或抽取芯棒的时间太晚,造成蜡模产生裂纹。
3.防止措施
(1)选用收缩率较小的蜡料。
对于低温蜡料,当选用62℃白石蜡代替58℃白石蜡时,可以减少其收缩率。或提高蜡料中石蜡的含量5~10%,即55~60%,也可减少蜡料的收缩率。或采用60℃白石蜡(含量95%)与低分子聚乙烯(含量5%)配制的蜡料,其收缩率约为1%,较低。
(2)控制压型、制模间和冷却水的温度。
对于低温蜡料压型的温度控制在18~25℃,中温蜡料压型的温度控制在20~24℃为宜。制模间的温度应控制与压型温度一致,冷却水的温度也应控制与室温一致;必要时制模间应安装空调,温度控制在20℃为宜。
(3)改进蜡模设计(即压型设计)。
改进蜡模设计,尽量使其壁厚均匀;壁厚不均匀应圆角过度(过度圆角应为“两个相邻壁厚之和”)的“1/5~1/3”);必要时可以增加工艺筋,把蜡模收缩时的应力降到不产生裂纹的程度。
(4)严格执行操作规程。
改进起模方法,必要时增加起模装置,避免蜡模在起模过程中产生裂纹。
严格控制蜡模冷却时间,一般为10~60min。蜡模冷却后应及时取出随蜡模一起冷却的芯棒,使其不能阻碍蜡模的收缩。
——本信息摘自网络未经证实,仅供参考